Advancements in RFID for Metal Manufacturing and Asset Tracking
RFID (Radio Frequency Identification) technology has evolved far beyond inventory management and warehouse tracking. Especially in metals manufacturing and hazardous production environments, RFID offers invaluable benefits that can optimize production, ensure safety and provide end-to-end traceability.
With the latest advancements in technology, such as hot labels and labels that resist toxic and dangerous environments, RFID has become an indispensable tool for manufacturers.
Advancements in Asset Tracking: Hot Labels and Resilient Tags
As RFID technology continues to evolve, offering new possibilities for efficient asset tracking, two cutting-edge solutions stand out: hot labels and resilient tags. Let’s explore how these technologies benefit manufacturers, particularly in metal manufacturing and hazardous production settings.
Hot Labels: Withstanding Extreme Temperatures
Hot labels are specifically designed for high-temperature environments. Whether you’re dealing with foundries, metalworking or other heat-intensive processes, hot labels provide options that you may not have had in the past. Here’s why they matter:
- Temperature resilience: Hot labels are designed to withstand extreme heat and, depending on the label and tracking solution, will provide readability and data integrity.
- Accurate asset tracking: Hot labels provide more precise tracking throughout the production cycle.
- Process efficiency: Hot labels reduce guesswork and manual data collection, providing information for better decision-making, workflow optimization, and improved efficiency.
Resilient Tags: Durability in Harsh Environments
In dangerous and toxic production environments, resilient RFID tags provide solution options. These robust tags offer increased durability and reliability under difficult conditions.
- Chemical resistance: Resilient tags provide greater resistance to harsh chemicals, acids, and corrosive substances.
- Adverse conditions: Whether it’s extreme humidity, dust, or abrasive surfaces, resilient tags can be designed to resist difficult conditions to provide necessary material tracking.
Solutions Designed for Challenging Production Environments
In the past, manufacturers would struggle with gaps in material tracking. Labels and tags couldn’t survive harsh conditions. But, today there are more tracking options. With the right solution, manufacturers can address these gaps.
Typically, manufacturers will come to a solution provider like the GO2 Partner’s Metals team with a challenge. That could be tracking materials even in high temperatures, preventing mixed metal errors in the pickling process, or preventing errors in label application. Using material solutions like resilient or high-temp labels, a better label applicator, or even the latest RFID technologies, the experts will design or customize a solution that address the challenge.
5 More Benefits of RFID for Manufacturing
Whether in metals, electronics, chemicals, food, plastics or textiles, manufacturers across various industries are leveraging RFID to enhance their business operations. Here’s how:
- Automation and error elimination: RFID is an Automatic Identification and Data Capture (AIDC) technology that minimizes the need for human interaction. Once implemented, the system can automatically identify objects, collect data, and transmit information to other systems. This automation reduces human error, allowing your team to focus on other tasks while still collecting critical data. In metals manufacturing and hazardous production environments, RFID ensures you can collect more accurate and comprehensive data without increasing costs or impacting production.
- End-to-end traceability: In the past, manufacturers often resorted to inefficient and error-prone methods to fill gaps in traceability, such as using chalk scratches on products or relying on guesswork. Now, with the advent of low-cost RFID chips and tags, it’s possible to achieve end-to-end traceability, even in extreme applications. This capability is crucial as more customers and regulations demand robust traceability. With RFID, you can easily pass audits with trustworthy data.
- Safety: Safety is a top priority in manufacturing, especially in hazardous environments. RFID helps improve safety by collecting critical production data and digitally tracking assets during dangerous operations involving extreme temperatures, harsh chemicals and dangerous mechanical operations. By handling data acquisition, RFID enables employees to avoid potential safety hazards. Furthermore, RFID can flag potential dangers in the workplace, empowering employees with data to prevent problems proactively.
- Real-time access to production data: One of the significant benefits of RFID is real-time information access. You can instantly know when inventory is running low or locate an asset within the warehouse. This immediate visibility eliminates delays associated with using outdated morning reports for production planning. With RFID, you can set up APIs and data integrations to automatically feed data to the systems you choose. Whether you’re using a mobile device or a computer, you can access real-time information on the location of materials or the production status of an order.
- Identify opportunities for optimization: The real-time data collected with RFID asset tracking provides an excellent foundation for optimizing production. For example, adding RFID to equipment can track tool usage to improve repair and maintenance scheduling. RFID tags on raw materials offer insight into material use and movement, supporting better scheduling and production planning. Additionally, asset tracking can identify production problems and operational delays, informing process improvements and changes before they are implemented in other production areas.
Get Started with RFID in Manufacturing
With increasingly competitive markets and greater demands from customers, there has never been more incentive to adopt this evolving technology.
Rather than taking on the risk and responsibility alone, a safer strategy is to find a partner and supplier who understands both RFID and its applications in manufacturing — able to provide best practices that can set your business up for success as you transition to RFID.
Start by implementing RFID in a small test area to see how to best customize your solution before rolling it out to other areas. Plan well-defined phases for the roll-out, so the work is manageable. Leave enough time and resources for each phase of the project to reduce pressure and problems.
With enough time and planning, and the right partner, you can leave outdated asset tracking in your past and quickly begin benefitting from RFID in your manufacturing processes.
Share this
You May Also Like
These Related Stories
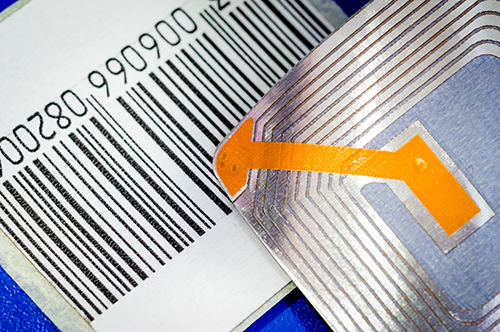
Guide to RFID Technology for Manufacturing

5 Ways Asset Tracking Improves Safety for Manufacturers
