5 Tips for Effective Warehouse and Production Signage
Effective warehouse signage may be the most efficient and low-cost way to improve operations efficiency.
Unfortunately, many facilities haven’t taken the time or effort to evaluate, improve or correctly implement signage for workers or guests. They put up just enough signs to meet regulations. The business relies on more experienced workers to teach new ones how to navigate operations, or just hope for the best. There is no best practice, no program, just a willingness to let things go until something breaks.
This is a lost opportunity. In an age where savings and a faster production time can mean the difference between profit and loss, there has never been a better time to implement or update your warehouse signage program.
What Is Warehouse Signage?
While we call it warehouse signage, it applies to many types of operational signage.
Successful operations, whether in a warehouse, a factory, a loading yard or shipping area, or even in a break room, require clear communication. You need to communicate where materials are located, provide warnings, and offer regulatory guidance on site or instructions on machine operation. Processes may change with a new inventory or machine, or there may be critical notifications.
Signage allows you to not only communicate change, but also reinforce safety procedures or best practices. Signage can prevent mistakes, reduce safety hazards and improve efficiency. It can help ensure your operation meets regulations, and shave valuable seconds from production time or shipping retrieval.
These benefits are well worth the time and investment needed to improve warehouse signage.
How You Can Improve Warehouse Signage
There are a few simple steps you can take to boost your warehouse signage and start seeing measurable improvements in performance.
Review Your Signage
Start by looking at your operational goals, and then identifying the most important information you need to communicate. If your goal is safety compliance, improving lean manufacturing, or an upcoming Six Sigma audit, then review if your current signage is supporting that goal.
For many operational leaders, it may feel like every goal is the highest priority. That’s fine, but what you need to do is be strategic in how you use the signage. Sometimes a smaller sign at the point where a compliance issue can occur may be more effective than a banner hanging from the ceiling. Reminder signs in a break room can help reinforce best practices better than a sign on the production line.
Identify Gaps in Your Signage Strategy
Sometimes, filling in the gaps in your signage is just as important as improving what you already have. Consider if you have signage in the following areas:
- Exit and fire signage
- Directional and wayfinding signage
- Warning and safety signage
- Machine safety and instructions signage
- Protective gear and wear signage
- Traffic and security signage
- Smoking policy signage
- Inventory and storage signage
- Material handling signage
Look at the areas where your operations struggle. Maybe bottlenecks or steps where you are seeing waste or inefficiency could be improved with better communication. These may indicate gaps in your signage.
Review Readability and Usability in Your Signage
You can have the best signage strategy in the world, but if workers and visitors can’t read the sign, then they aren’t doing you any good. Poorly made signs or ones that are provided by a printer that isn’t experienced in warehouse or operational signage aren’t providing a benefit. This can lead to users ignoring the sign. Make sure to use a print resource with experience in operational signage.
OSHA/ANSI provides clear guidelines, including using pictograms and legible, bold text. There are guidelines for color-coordinated text and imagery for warnings and hazards. Make sure you follow guidelines for signage in the following areas:
- Hazardous areas: Reminders for potential hazards, such as new power generators or traffic areas near machinery.
- Safety equipment: Signs and labels on heavy or potentially dangerous machinery, which should include reminders of safe practices and safety equipment.
- Emergency signage: Fire extinguishers, eye wash stations, first aid kits, emergency shut-offs and, most importantly, emergency exits should all be labeled.
- Safety reminders: Review common injuries in the workplace and utilize signage to help prevent them. For example, a quick reminder about safety requirements on heavy machinery can prevent injury.
Standardize Your Signage
When building a signage strategy, it’s easy to start creating signs without considering standards. This can lead to variability and confusion. Saving time with a sign doesn’t work if the user needs to spend valuable seconds translating the information.
The OHSA/ANSI guidelines and pictograms are a good place to start. Make sure to incorporate these in your signage where possible. Also consider color-coordinating signs. Standard colors on signs include:
- Black and white: Hazardous areas, or safety and compliance warnings.
- Black, blue, and/or green: Work station, raw materials or inventory.
- Blue and white: Protective gear or wear warning and safety policies.
- Green and white: Safety instructions and emergency equipment.
- Orange: Work station, raw materials, inventory or hold for inspection.
- Red: Work station, defective materials or safety warning.
- Red, white and black: Danger, and electrical, safety and fire hazard areas.
- White: Work stations, equipment or permanent fixtures.
- Yellow: Work stations, traffic lanes or aisles
- Yellow, white and black: Caution, hazardous areas or equipment.
Even in the standards, there is some variability in the use of colors. A good best practice for facilities is to create a standard signage document that tracks how colors, icons and pictograms are used in the facility. This can be referenced to identify discrepancies and for any new signage that needs to be created.
You can also discuss your needs with a printer experienced in operational signage. They can provide insight and best practices from their experience with other facilities.
Utilize the Right Materials
There are a few things to consider as you select and implement your sign program.
Is your sign durable enough for the environment you are posting it in? For many production environments a paper sign just won’t last. You need a sign that will deliver reliable information over time. This means you need a durable material designed to deliver even in potentially wet, dry, cold, toxic or dangerous environments.
Floor signage is another item to consider. The floor is a large blank slate, but you need the right signage for it. Look for signs made of slip-resistant material. Also consider the environment. If the area is wet, a sign on the floor can be a slip hazard. Readability is another thing to consider. Depending on the lighting, you may need a glossy or matte finish to make the sign easy to read and not be distracting.
Not all signs are created equal. A little research can ensure you have a sign that lasts and works for your facility.
How to Start a Warehouse and Production Signage Program
The questions and information we’ve provided here will give you a good place to start when evaluating the operational signage in your facility.
If you aren’t seeing the results you expect from your signage program, we suggest reaching out to a printer experienced with warehouse and production signs. They’ve delivered results, and may have insight and best practices that can make a difference for you. In addition, because they’re already producing the specialized signs, they can often give you a better price than other suppliers.
If you have questions, or want to talk to an expert with experience in warehouse and production signage, then contact GO2 Partners today. We’re here to help.
Share this
You May Also Like
These Related Stories
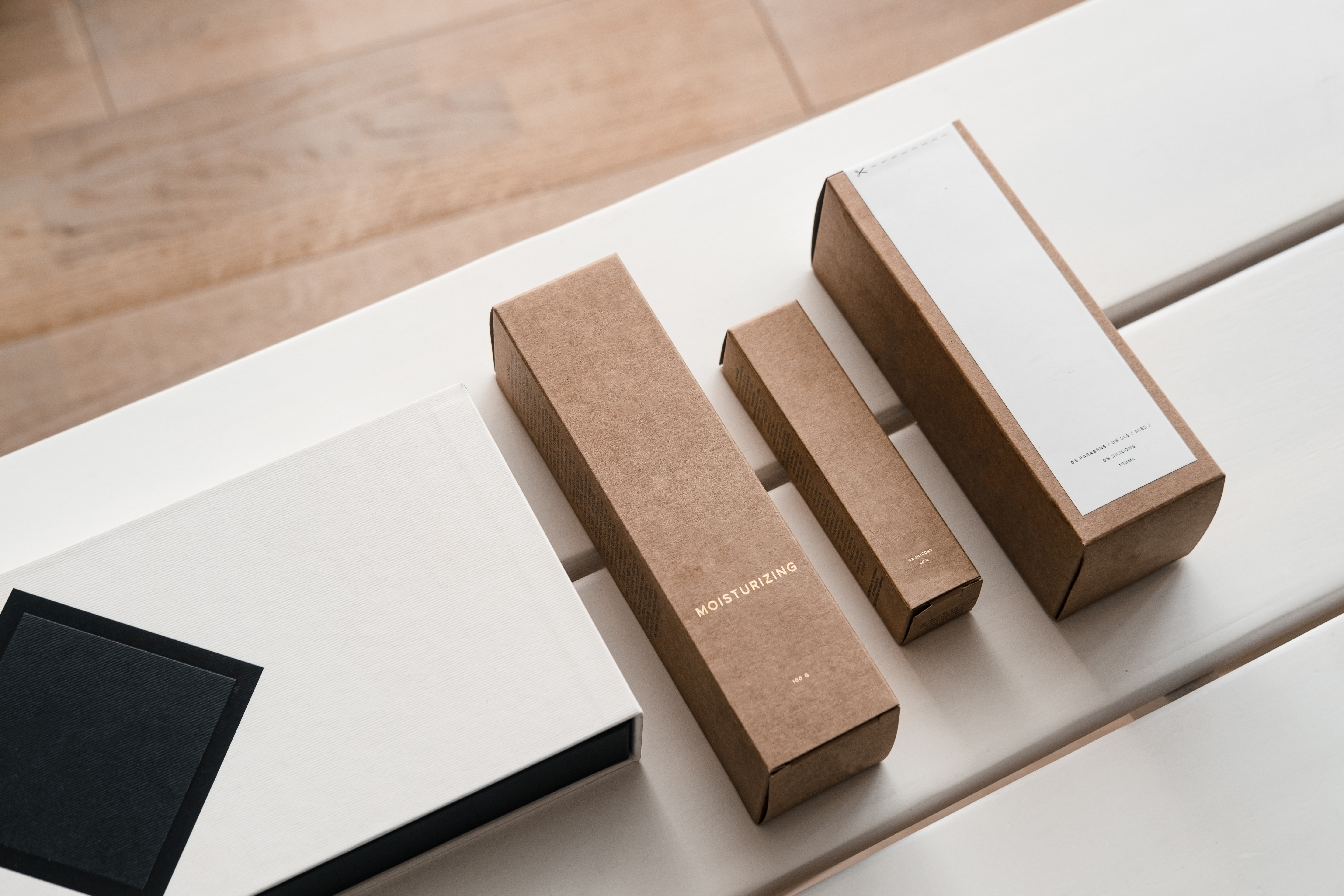
7 Ways You Can Improve Your Product Packaging

How to Use Managed Services for Your Business
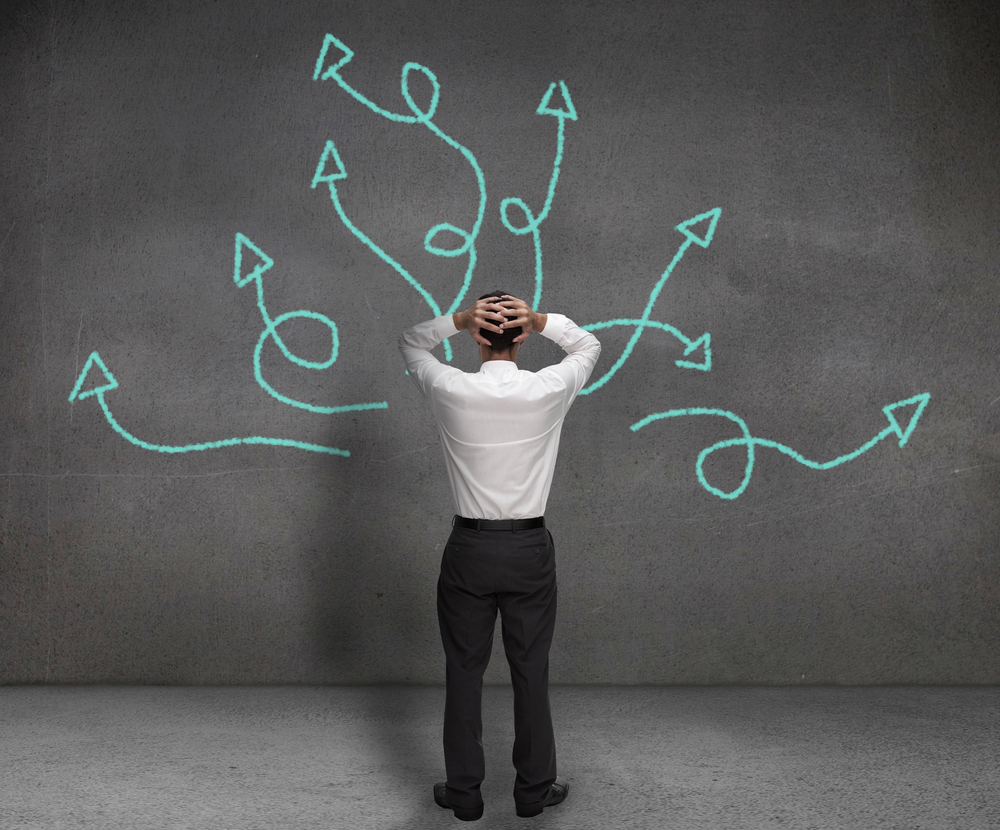